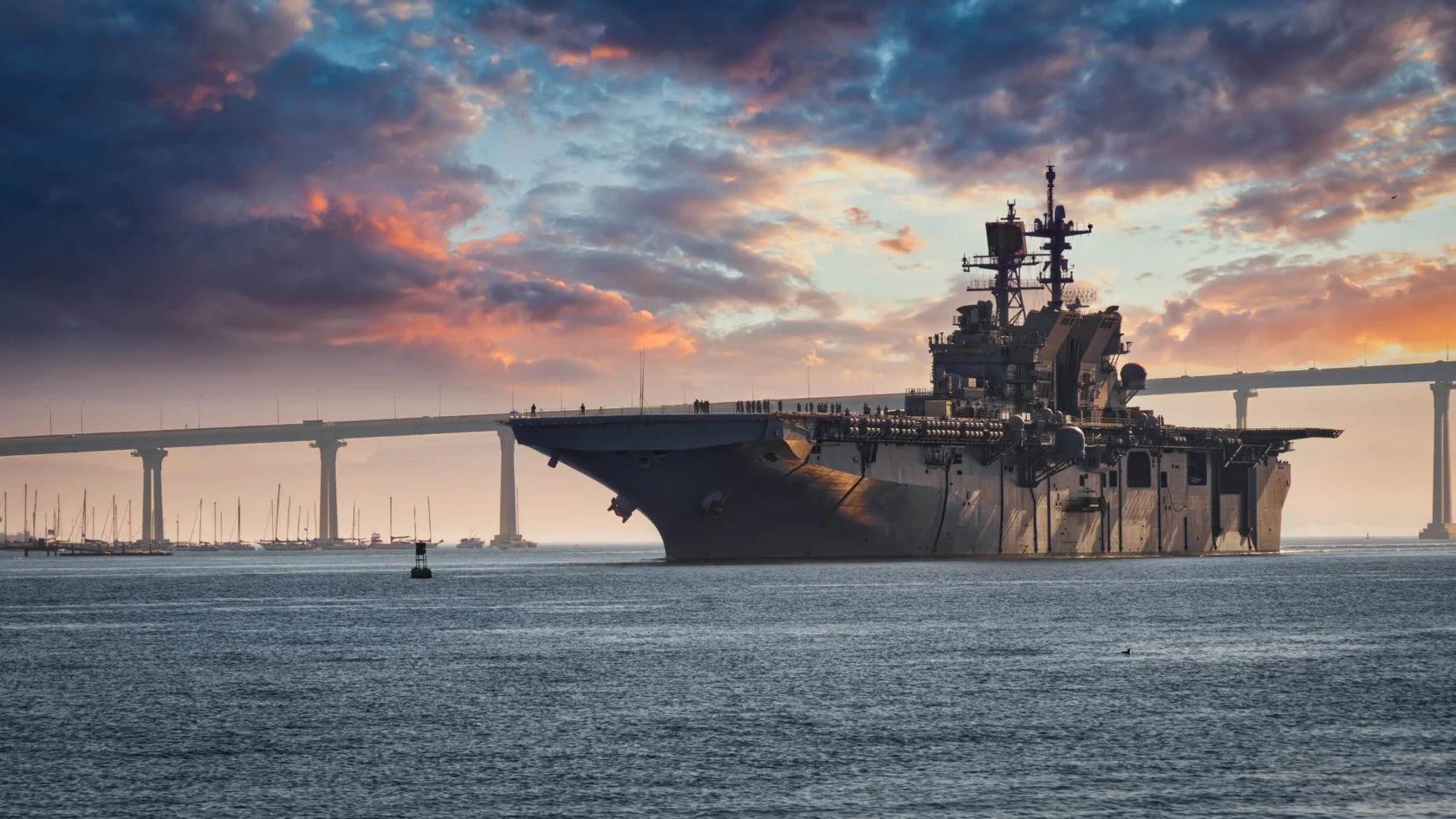
Life Cycle Engineering
Every Operation Can Be Reliable & Efficient
Implementing world-class asset management, reliability, maintenance, workforce development, and engineering solutions since 1976.
Who We Are
For decades, the U.S. military and industrial operations have trusted LCE to improve risk management, reliability, and productivity.
By partnering closely with clients, LCE not only enhances operations but also strengthens team capabilities with its “guide by the side” approach—empowering people and organizations to reach their full potential.
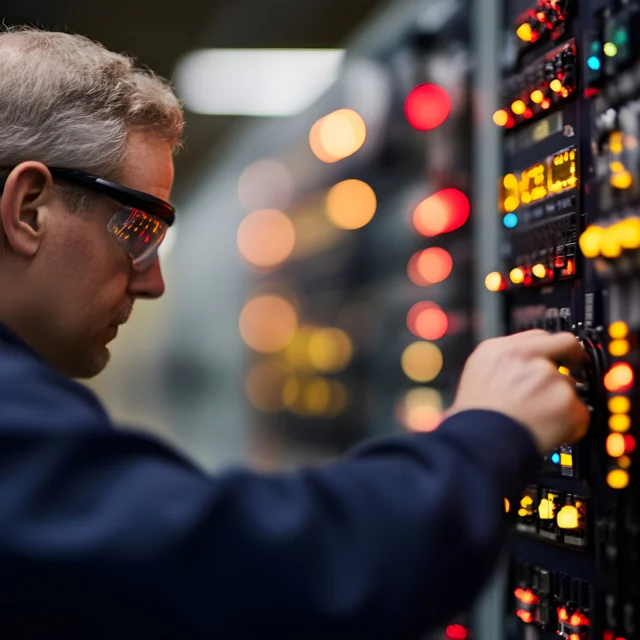
Our Approach
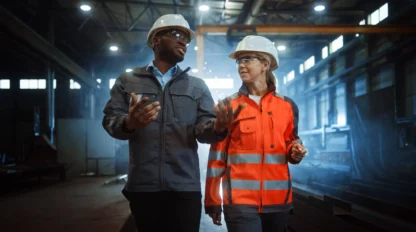
People
At the heart of every successful operation is a skilled and engaged workforce. LCE’s approach focuses on empowering your teams through consulting, workforce development, and hands-on training. From university-backed certifications to coaching in reliability, engineering, and asset management, we ensure that your people are equipped to drive sustainable performance and lasting change on the deck plate or at your facility.
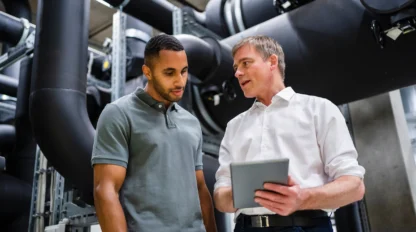
Process
Effective processes are the backbone of operational excellence. We tailor our methodologies in reliability, process excellence, and asset management to meet your organization’s unique needs. This enables continuous improvement, enhancing efficiency, quality, and cost effectiveness, and unlocking the full potential of your operations.
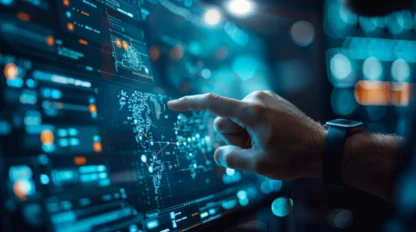
Technology
In an increasingly digital world, leveraging the right technologies is critical. LCE supports your transformation with smart manufacturing, digital modernization, and information warfare solutions to optimize your software landscape. From IT and cybersecurity to marine and logistics services, our approach ensures your technology drives innovation and operational success.
Industries We Serve
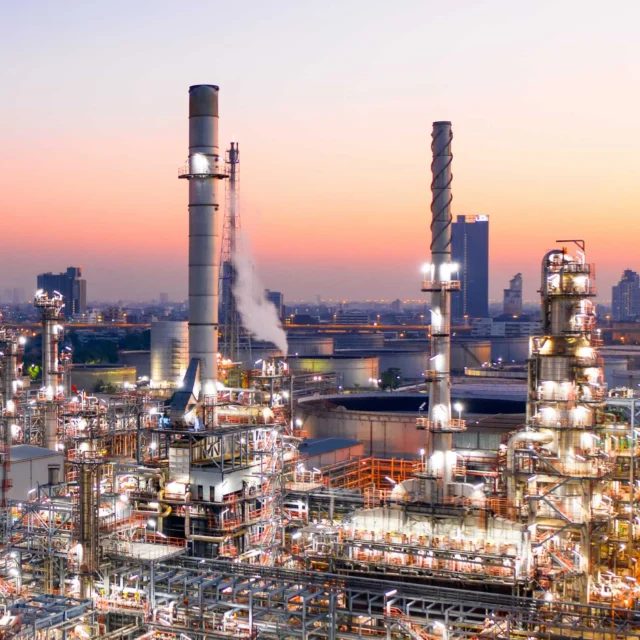
Take the Next Step
Take the first step toward operational excellence. Contact us to learn how LCE can provide the guidance and solutions you need.