Reliability Engineering, Risk & Productivity
Life Cycle Engineering’s reliability engineering and risk management services help optimize asset performance, reduce risk, and ensure smooth operations. By improving asset condition, upskilling teams, and addressing issues proactively, we enhance efficiency, extend asset life, and drive long-term sustainability.
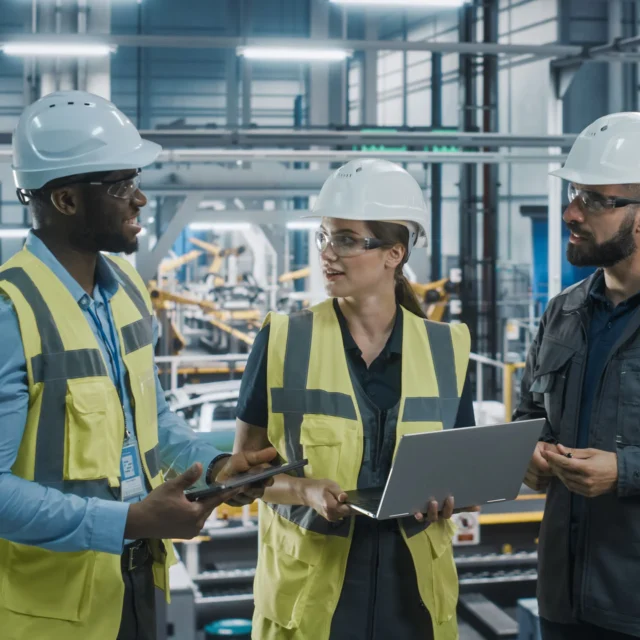
What we do
Reliability Engineering and risk management services enhance systems, develop strategies and reduce costs
Our experts will collaborate with you to create a risk-based asset management system that prioritizes resources for critical issues, builds a framework for continuous improvement, and helps meet business objectives, including regulatory compliance.
Optimize asset performance and minimize risk with a customized RBAM® strategy to meet objectives
LCE’s RBAM methodology integrates risk management, standard work practices, and condition-based maintenance to allocate resources based on process criticality. This approach establishes controls and utilizes reliability analysis for continuous improvement.
Our strategy includes cataloging asset attributes, creating functional hierarchies, conducting criticality and failure analyses, and developing control plans to safeguard assets while optimizing operational performance. Our asset functional hierarchy (taxonomy) approach follows the ISO 14224 standard, adapted to your organization.
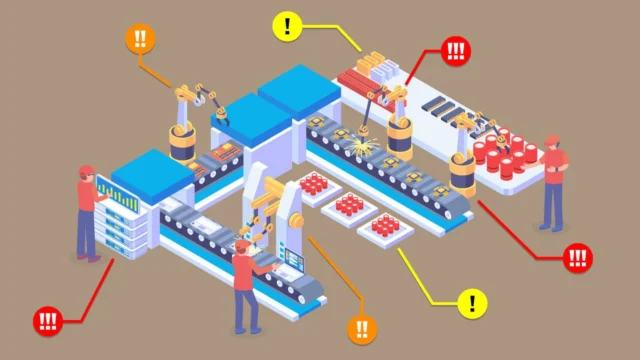
Reliability, Availability, and Maintainability (RAM) modeling identifies production loss causes and mitigates risks
Assets often lack consideration for all failure modes, leading to suboptimal performance and unmet goals. Our reliability engineering experts work with site teams and vendors to conduct a RAM analysis, pinpointing weaknesses to boost efficiency, reduce downtime, and optimize maintenance.
Our approach includes functional block diagrams, reliability data analysis, production requirement evaluations, maintainability assessments, and risk mitigation strategies. Redundancy and design robustness are also considerations during the RAM analysis process.
Apply Reliability Centered Maintenance (RCM) strategies to ensure critical assets maintain functionality
Without optimized operations and maintenance tasks, critical assets may lack essential care. Our experts apply RCM at any life cycle stage—concept, design, or operation. We collaborate to identify priority assets, gather relevant data, and conduct field inspections.
We can execute this work for you or with your team to establish risk rankings, create an FMEA with mitigation strategies, and provide a final report with actionable maintenance plans. Our FMEA approach follows the IEC 60812 standard for detailed equipment analysis.
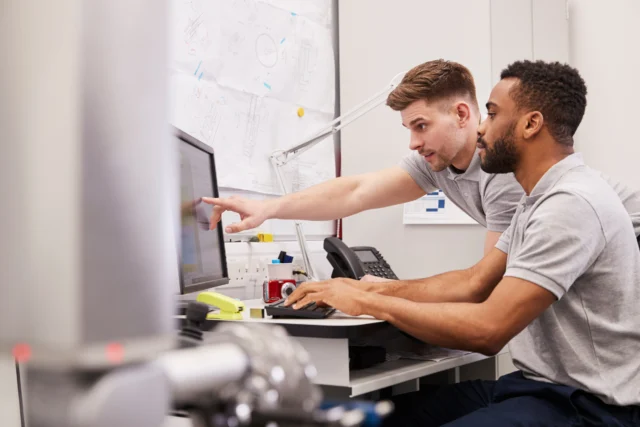
Skilled reliability engineers solve quality, reliability and cost issues with RCA and loss elimination
Our experts lead RCA and loss elimination programs to target waste and limiting factors affecting plant performance. We mentor teams, fostering continuous improvement. By analyzing historical performance and comparing it to best-in-class data, we identify loss elimination opportunities.
We conduct RCA on top issues, develop feasible solutions, and measure results, ensuring ROI and standardizing improvements for broader application. We understand physical, administrative, and human causes while searching for ultimate latent causes to correct future occurrences and systemic failures.
Drive asset value with expert mentoring in RCM, loss elimination, maintenance planning and risk management
Our reliability engineering approach focuses on optimizing maintenance processes to minimize downtime and enhance reliability. By systematically identifying and addressing root causes of production losses, we ensure consistent output.
We integrate failure mode-based maintenance plans to target specific equipment vulnerabilities, reducing the likelihood of breakdowns and extending asset life. Incorporating total cost of ownership in capital projects safeguards long-term value while actively managing risks that could impact operational continuity and performance.
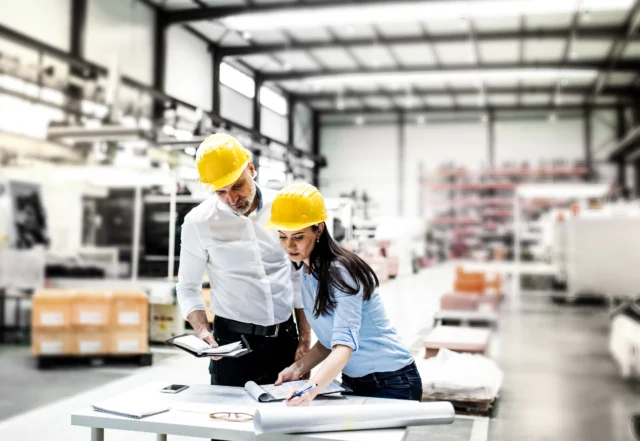
Equipment Bill of Materials (BOM) Development Services provide detailed documentation of equipment components
By creating a comprehensive BOM, we ensure streamlined procurement, efficient maintenance planning, and reduced downtime. Accurate bill of materials (BOM) reduce the chances of buying incorrect parts, minimize research time and provide easy access to required material data.
Our experts catalog parts, materials, and specifications, ensuring your operations have the right resources at the right time to keep equipment running efficiently. LCE’s BOM development services improve work planning and execution, saving time and money, and ensuring uninterrupted productivity.
Our services include acquiring BOM documentation, validating existing BOMs for accuracy, integrating BOMs into CMMS/EAM, and establishing a standard process for managing updates.
Start a capital project with operational excellence
Our Operational Readiness experts help you deploy capital effectively, optimizing total cost of ownership from concept to disposal. Services include:
- Operational Risk Assessment: Identify risks from design to steady-state operations, enabling strategic, cost-effective mitigations.
- Integrated Master Schedule (IMS): A unified tool for planning, executing, and tracking project activities.
- Checkpoint Process: A structured roadmap to identify, remedy, and validate deliverables for project startup readiness.
- Reliability and maintenance integration into the project management and asset delivery processes.
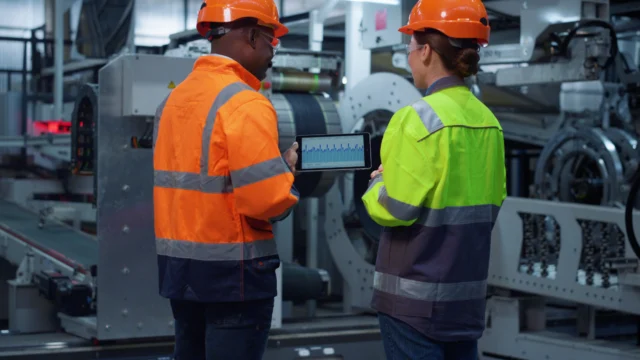
Obsolescence Management ensures critical components stay available, preventing downtime from obsolete parts
Our experts design a comprehensive program that includes a detailed audit to find at-risk components, evaluating lifecycle status, supplier viability, and operational impact. We work with your team to develop a strategic action plan—whether sourcing alternatives, redesigning systems, or securing last-time buys.
Proactive monitoring tracks part lifecycles, maintaining operational continuity and efficiency. Facility condition assessments are a form of obsolescence management that our experts will conduct to help identify infrastructure risks and help build comprehensive strategic capital investment plans and site master plans.
Asset Criticality Assessment prioritizes assets by impact and risk to guide maintenance and resource decisions
Our reliability experts assess assets to enhance decision-making, optimize maintenance for critical assets, and reduce costs. They define plant-specific criteria, gather relevant asset data, and train your team on the assessment process. Following the assessment, they compile a criticality listing and submit a final report for easy integration into your database.
Equipment and maintenance master data includes manufacturer, model, serial number, critical spare parts, non-stock spare parts, instrument calibration points and many other parameters. LCE has developed templates for efficient upload of master data to most common CMMS platforms including SAP PM.
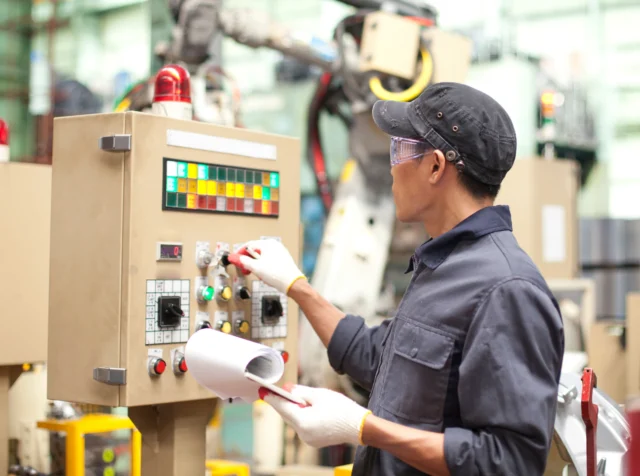
Line Performance Optimization® (LPO) services solve chronic reliability issues in processes or manufacturing lines
Our Line Performance Optimization (LPO) services tackle common reliability issues like unplanned downtime, ineffective maintenance, lack of standardized processes, quality concerns, and material flow inefficiencies. By using our LPO approach, clients have boosted OEE by 5% just focusing on a single limiting unit operation, saving millions and unlocking hidden availability; double-digit OEE improvements have been realized when focusing on an entire line of connected operations.
Our lean experts focus on problem-solving tools like value stream mapping, FMEAs, and Pareto analysis, while integrating change management to ensure workforce engagement and sustainable results in optimizing equipment and processes.
Ready To Maximize Asset Performance?
Testimonials
Take the Next Step
Harness the full potential of your assets. Partner with LCE today to implement tailored reliability solutions that drive performance and sustainability.