Engineering Design & Manufacturing
Life Cycle Engineering provides engineering design services to Federal and commercial clients worldwide. Our experts specialize in mechanical, electrical, structural, and software engineering, from concept and design to feasibility, prototyping, and testing. We also reverse engineer systems to enhance functionality.
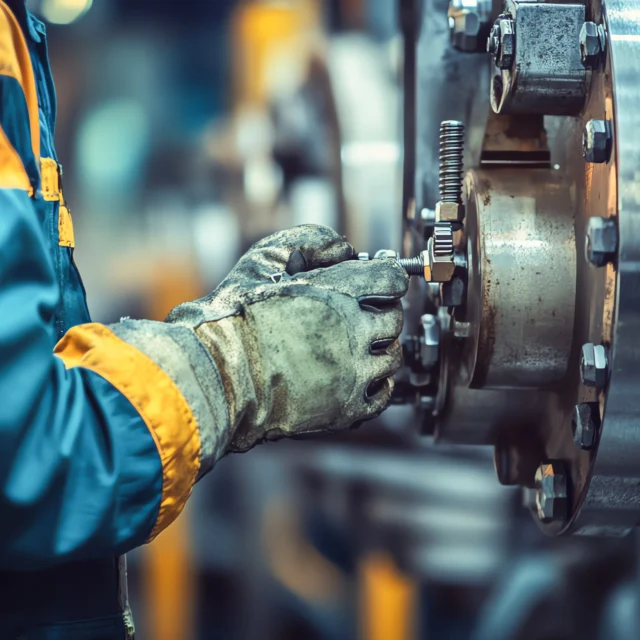
What We Do
Our experts conceptualize, design, troubleshoot, and reverse engineer technical solutions
Developing models and drawings to inform system design
Our designers and drafters develop 3D models, detail drawings, fabrication drawings, modification drawings, diagrams, and figures for use in technical manuals. Our experience includes CAD support for multiple engineering disciplines (i.e. piping, electrical, HVAC, structural) relating to various phases of ship design, industrial design, and mechanical design activities.
Additional experience includes ship checks and field verifications to obtain design criteria onboard ships and at commercial facilities. This includes creating sketches of existing system modifications and redlines of existing drawings to reflect modifications and updates. We utilize 3D notional and design models to develop images and videos for use in presentations and design reviews to ensure our customers’ design concepts/criteria are being met.
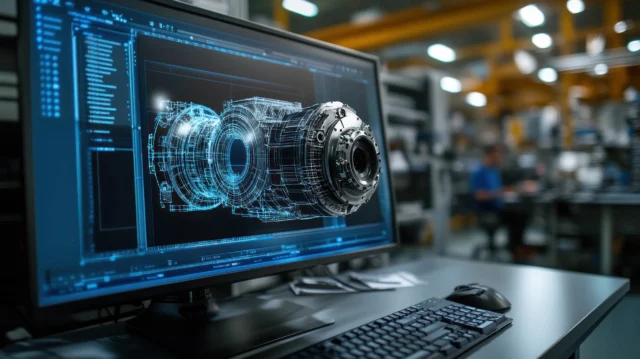
A quick turn analysis of the cause of failure and the actions necessary to prevent future failure
We have analyzed numerous components for our clients including: diesel engine journal bearings, crankshafts, pistons, cylinders, connecting rods and bolts; gas turbine compressor and combustion section blades and vanes; ball bearings; and various fasteners. Because of our mechanical design expertise we can provide recommendations for changes in component design or operating parameters.
We can also coordinate the failure analysis with stress analysis, fatigue and fracture mechanics analysis, and computational fluid dynamics analysis to provide even more definitive results.
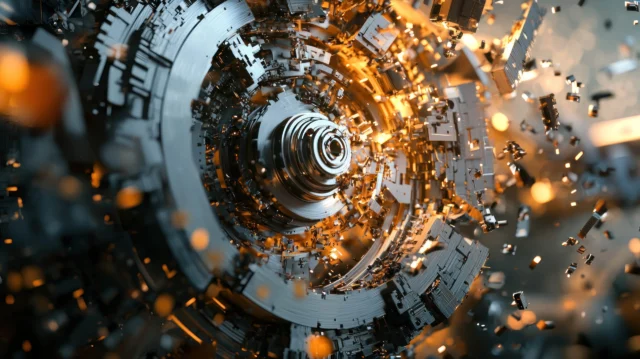
Validating and testing design behaviors of DoD and commercial equipment
Our engineers conduct finite element, shock, vibration, seismic and structural analysis of commercial and military equipment to predict how it will react to real-world forces. We use advanced FEA software to simulate designs under various conditions to determine potential failures and help optimize designs.
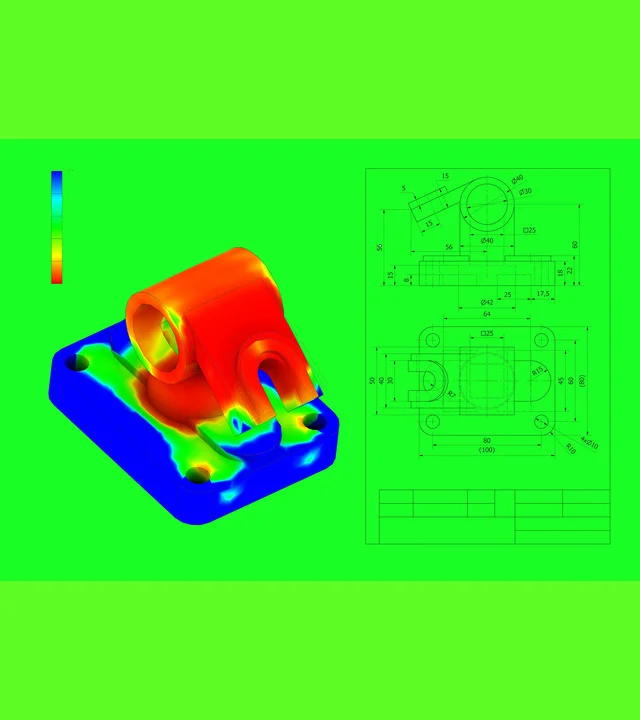
We optimize systems, reduce downtime, and extend asset life to ensure long-term performance
Studies show that over 80% of an asset’s reliability and total cost of ownership is set during design, build, installation, and commissioning. Yet site teams, who will operate and maintain the equipment, often have minimal input.
LCE’s design for reliability process identifies critical design parameters, predicts potential failure rates, and develops specifications to ensure assets perform as intended for their planned life. We can help make critical decisions regarding redundancy, robust equipment design and the financial analysis to make the best choices regarding system design.
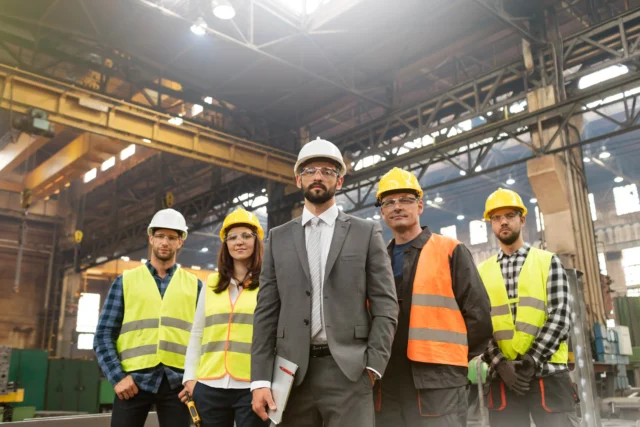
Ready To Optimize Your Operations?
Take the Next Step
Let us design your next solution. Reach out to our experts in engineering design and manufacturing today.