A Reliable Operation Is More Efficient, Safe, and Standardized
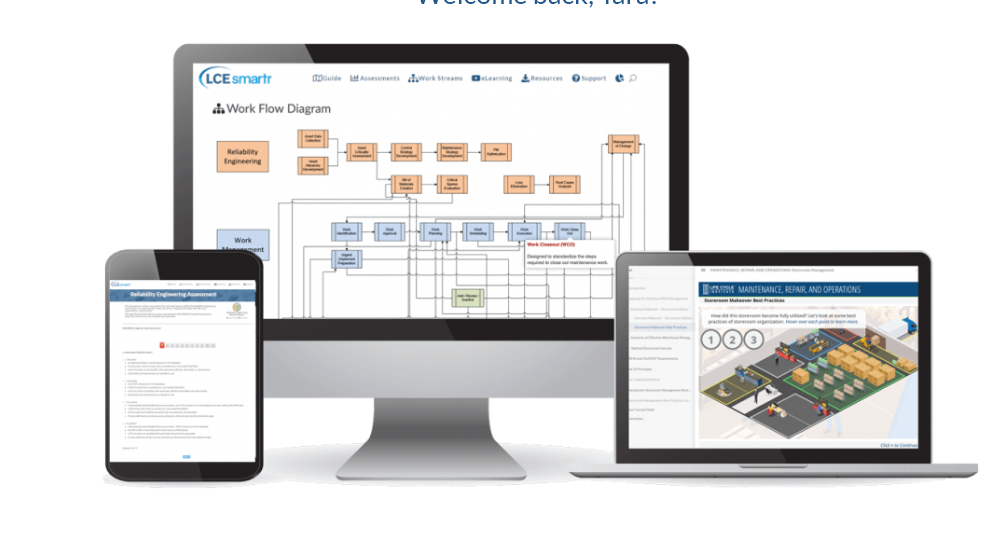
With the LCEsmartr Playbook system, global pharma manufacturer runs more reliably and efficiently.
Our client, a global leader in the pharmaceutical sector with 30 manufacturing facilities and a workforce of 50,000+, recently grappled with standardizing reliability and maintenance practices at scale. One of the biggest challenges of expanding manufacturing operations through mergers and acquisitions are alignment and maintaining standards across sites.
Building a team around a shared reliability goal
While expanding through strategic mergers and acquisitions can add depth and skill to your bench, it also brings challenges. Consider a sports team – each player has their own gifts to contribute, but they also bring their own handicaps and baggage. It takes a skilled coach with a solid approach to bring everyone together as a single team, one that approaches their work with the same goal, effort and consistency.
In the case of our client, the company’s leadership sought to implement standardized reliability best practices, tools and training to establish a common baseline and unify their team.
Identify their North Star: Operational Excellence
With the goal of improving operational excellence and strengthening research and development capabilities, this pharma leader wanted to:
- Level-up and harmonize reliability across global operations
- Reduce downtime and operational risk through better work practices
- Extend asset life cycle and better manage related cost of ownership
- Improve safety and meet regulatory requirements
- Strengthen the organization’s ability to adapt to change
- Establish a management system with controls for asset management documents, processes and content
Putting the Operational Excellence plan into play
Our client identified the need for an operational support system to help address these challenges in a sustainable way. The LCEsmartr Playbook was selected because of its ability to accelerate adoption of their business goals and provide a central location for essential resources for employees. Their LCEsmartr Playbook was curated with materials aligned to their objectives, including:
- An implementation guide for more efficient adoption of best practices
- Organizational change management tools to empower leaders in championing reliability transformation
- Work process models to establish common language around operational reliability and enable sharing across the organization.
- Standardized work templates to promote a life cycle asset management mindset
- Online reliability training for efficient employee on-boarding, reskilling, and up-skilling
Early in the process, several leadership team members also participated in Life Cycle Institute’s Reliability Excellence for Managers training.
With training support and the LCEsmartr Playbook, our client successfully implemented their tailored LCEsmartr Operational System. In addition to standard services, they received customized tools and resources, including implementation guides, change management tools, work process models, standardized templates, and online training modules, which enabled them to drive operational excellence and succeed in their reliability and maintenance initiatives.
Reaping the operational rewards
Leadership hailed the transformative effect of standardized practices and customized implementation, emphasizing the company’s commitment to continuous improvement and excellence.
Employees embraced the new LCEsmartr Operational System. Over 492 active users completed more than 900 classes, logged in more than 5,000 times and downloaded resources over 3,800 times. As a result of high engagement, there was a notable decrease in downtime and increase in productivity in manufacturing operations.
Summary
A global leader in the pharmaceutical sector with 30 manufacturing facilities and a workforce of 50,000+, recently grappled with standardizing reliability and maintenance practices at scale after expanding operations through mergers and acquisitions. The company’s leadership sought to implement standardized reliability best practices, tools and training to establish a common baseline and unify their team.
With LCE’s support and a tailored LCEsmartr Playbook rollout, our client saw a transformation in their operations’ reliability and maintenance practices, and widespread commitment to continuous improvement and excellence, resulting in measurable improvements in operational efficiency and employee engagement.