Accelerating Progress in a Manufacturing Plant’s Reliability Journey
solutions
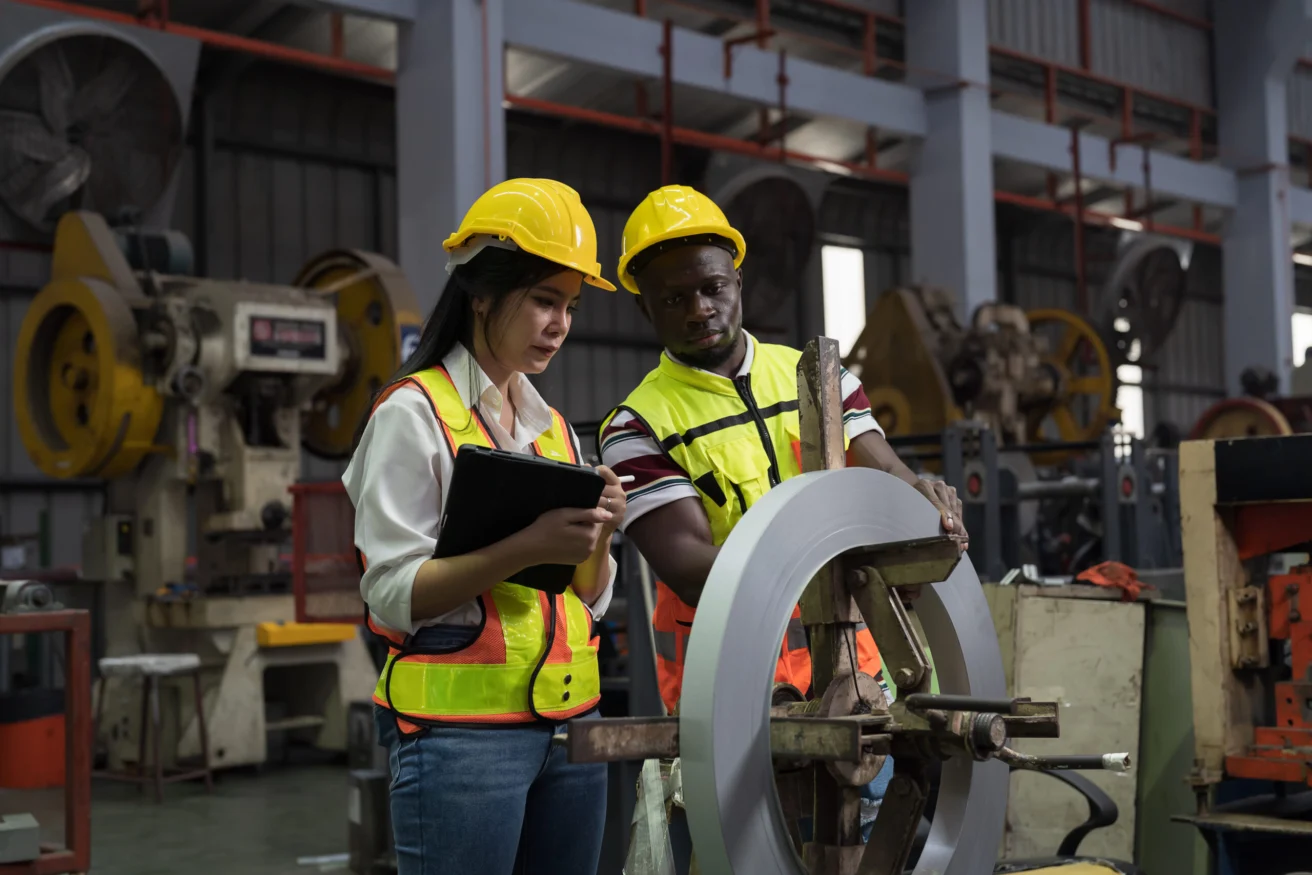
Accelerating Progress in a Manufacturing Plant’s Reliability Journey
Improving reliability in an asset-intensive manufacturing plant is often described as a journey because it can take multiple years to drive measurable improvements. In the case of this metal products plant, the reliability journey took some twists and turns, but progress continues.
Background
This mid-size plant was a relatively strong performer in the corporation. Good leadership focus on key production parameters had yielded progress in scrap reduction and yield. A solid leadership team was able to focus and execute on initiatives and the plant was turning the corner from years of non-profitability. In particular, the site enjoyed very strong leadership from the Plant Manager who spent a lot of time on the floor and was a real driver for success. The Reliability Excellence Assessment performed at the site resulted in a score of 516, placing them in the upper portion of the Emerging realm.
The one major area where the plant had not made significant progress was in reducing downtime due to mechanical and electrical issues. They partnered with Life Cycle Engineering (LCE) to focus on their processes and execution in Work Management, Materials Management, and Reliability Engineering. Another focus area was engaging with plant leaders to provide the necessary level of implementation support and to create the ongoing cultural environment for a process-mandatory workplace.
Leadership and Change Efforts
To create the necessary foundation for implementing new approaches and new processes, LCE provided coaching on leadership and change. The goal was to equip plant leaders to create the necessary level of sponsorship for the improvement effort; lead plant employees through the predicted aspects of organizational change; and work through anticipated barriers and resistance to change.
Work Management
LCE’s efforts to improve how the plant approached work management focused on the entire process from identifying work all the way through to work execution. This work touched many stakeholders in the site but an emphasis was placed on Planning and Scheduling personnel. Improvements to work management consisted of developing and establishing eight processes covering these areas:
- Work Identification
- Work Approval
- Work Prioritization
- Work Planning
- Work Scheduling
- Work Execution
- Work Closeout
A cross-functional team developed the processes. Leaders and plant personnel were trained and the processes were “turned on” in early 2018. Key work management metrics were developed, captured and reviewed to drive improvement in how the processes functioned.
Materials Management
LCE’s efforts to drive and support changes in the management of MRO materials at the site focused on the central MRO warehouse and associated personnel. The Materials Management work consisted of establishing key Materials Management processes. A cross-functional team was established to develop key Materials Management processes in the following areas and train the various stakeholders on their role in using them.
- Planned Work Purchasing
- Expedited Purchasing
- Storeroom Receiving
- Inventory Stocking
- Satellite Stores Stocking
- New Item Set Up
- Inventory Issue
- Cycle Counting
- Return to Inventory
- Return to Supplier
- Kitting for Planned Jobs
Reliability Engineering
The plant did not have a reliability engineering function, although a few months prior to LCE’s involvement the plant had promoted someone into the role of Plant Reliability Engineer. While he had some maintenance experience and had run their lubrication program, he lacked experience in basic reliability engineering processes.
LCE established a cross-functional Reliability Engineering team to develop processes and train stakeholders in how to apply them. Because we were teaching as well as establishing processes, we developed the process, selected a portion of the plant to apply the process to, and then developed competency by demonstrating how to apply the process. This helped the larger team understand the processes and taught the reliability engineer how to administer the processes and facilitate the work in these areas:
- Root Cause Analysis
- Loss Elimination
- Asset Hierarchy Development
- Control Strategy Development
- Maintenance Strategy Development
- Preventative Maintenance Optimization
Challenges to Implementing New Processes
Aside from the usual resistance to change and normal learning-curve difficulties, there were two situational challenges: the existing organizational design and a significant change in leadership at a key point in the implementation.
Organizational Design – The existing organizational design was ill-conceived to support reliability processes. LCE partnered with plant leaders and the Human Resources function within the plant to remedy the problem in three phases: assessing current roles, defining future roles and defining the transition path for each impacted individual.
New Plant Manager – Approximately three quarters of the way through the project, right at the time most processes were being implemented, the existing Plant Manager was promoted and the new plant manager was selected from within the existing site personnel. This caused significant distraction and a loss of momentum as the site digested the significant change.
Eight Months Later, a Progress Check-in
Eight months after completion of on-site support, and approximately one year after the new processes were implemented, LCE’s engagement leader performed a follow-up visit to see how the plant was progressing on their reliability journey. Significant progress had been made in key areas:
Work Management (Planning and Scheduling)
The team was continuing to develop organizational competencies in Work Management. Their Maintenance Planner had made substantial progress and was performing at a high level in preparing planned jobs for execution by the Maintenance staff. Although they were working through typical issues like prioritization of urgent work, PM completion and capturing craft feedback on work orders, the team was making good progress in many areas. They were still focused on:
- Work management processes
- Improving the re-buildable components process
- Improving the urgent work prioritization process
- Planner competency and coordination with other key areas
- Scheduling meeting discipline
- Driving improvement through the cross-functional team
- Using Work Management metrics to drive improvement
Materials Management
Substantial progress was made in the MRO storeroom during the time LCE was on site. An action plan was established and key items were executed with the former plant manager driving for rapid execution of improvements including lighting upgrades, reorganizing the MRO warehouse to optimize flow, a better-defined kitting area and upgraded racking that included capacity and load ratings.
The site hired a new Warehouse Coordinator to further drive warehouse improvement. The accuracy of cycle counts and location had improved. Housekeeping of the area had improved and the area labeling was much better. Staging of kits for craftsmen had significantly expanded and it was being well received by the craftspeople. When asked about this, one craftsman remarked “Kitting is working great! Our jobs are kitted and ready to go…they save us a ton of time…hours used to be spent searching the storeroom!”
Reliability Engineering
In the follow up visit, it was evident that much progress had been made in the proliferation of reliability engineering processes. The Reliability Engineer’s competency and experience had matured. Asset hierarchy had been completed for all assets at the site, root cause analysis was being conducted of triggered events, and the lubrication program had been organized.
There was more work yet to be accomplished in the evaluation of Preventative Maintenance tasks and development of Equipment Maintenance Plans for the critical assets at the site. However, the personal growth of the Reliability Engineer was plainly evident in his confidence and his growing reputation among his peers.
There are Always New Challenges
The plant had a very challenging year in 2018. Two major challenges were impacting the plant: a high level of plant utilization and operational issues with equipment programming.
Loaded to capacity and beyond – The healthy economic environment in 2018 drove strong demand for the corporation’s products. This resulted in heavy production demand for the plant, testing its resolve to perform required PMs and allow time for corrective maintenance to be performed.
Programming problems – The plant was supported by central engineering for its control logic and manufacturing control systems. Changes made to the systems created a substantial amount of equipment malfunction and downtime as the plant worked through these changes and their implications.
Conclusion
Reliability journeys extend for years, not months, and every journey has its own victories, setbacks, and headwinds. Yet as this example shows, with the appropriate levels of leadership and support, a site can accomplish a lot in a year. Successful journeys are fueled by leadership expectations, grounded in a reliability-based value set, which drive people and their performance to a higher level.
To learn more about a Reliability Excellence Assessment,
please visit www.lce.com