An Aluminum Cast House Throughput Study Identifies Strategies to Improve Output by 13%
solutions
sectors
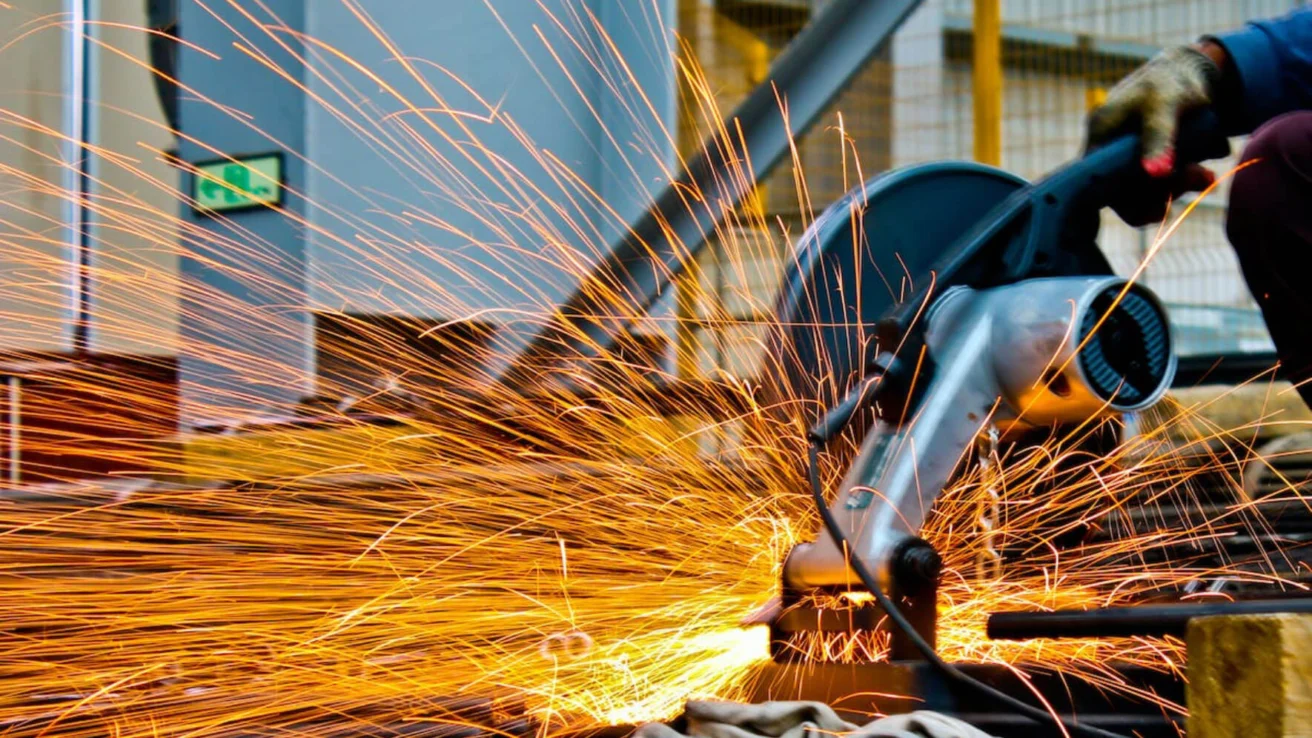
Aluminum Cast House Throughput Study
Situation
An aluminum producer needed to increase production capacity. It turned to Life Cycle Engineering (LCE) to help with a specific issue: identifying how the aluminum plant cast house could increase throughput to meet the increased demand for aluminum billets.
Solution
Producing aluminum is a complex process with multiple stages that take place in the cast house: melting, transferring the molten metal, treating it, and then casting it into different shapes. LCE’s solution began with an on-site assessment of the current state of the process to provide an in-depth study of its throughput capabilities. The scope of the project was to:
- Review and understand operational / delay data impacting throughput
- Develop and share “quick wins” / opportunities to focus on immediately
- Develop a current-state map of the casting process
- Provide suggestions based on historical data, and recommend new technologies that would reduce current constraints /bottlenecks affecting overall output abilities.
Over a three-month period, LCE’s subject-matter expert gathered and reviewed data, and discussed the findings with operations personnel. He created a value stream map to show current bottlenecks and performed time studies on each of the process areas associated with the operation. Multiple studies were used to help identify and verify all of the constraints within the process, including roughly 30 hours of video, physical time measurements, and product travel analyses.
Results
After analyzing these studies, LCE provided plant leaders with these recommendations for operational improvements:
- Manage day-to-day operations using the simple process of hour-by-hour walks. Supervisors should develop their own shop-floor path to physically walk every hour to capture all deficiencies to output during that hour. A key enabler for this process is hour-by-hour boards at each processing point where operators capture actual output vs. target and write this down on 3’ x 4’ white board laid out in a simple grid pattern.
- Monitor breaks and lunches to ensure shop floor personnel are returning to their processes in a timely manner.
- A floater or supervisor should cover breaks and lunches to ensure the process is never impacted by not having an operator available.
- Track these key metrics by each operation area:
a. Operational and Maintenance delays
b. Mean Time Between Failures and Mean Time to Repair
c. PM and Schedule Compliance - Improve operational process times based on the specific findings from the individual process area studies.
Implementing these recommendations could potentially yield a 13% improvement in throughput with minimal capital expenditure.