By Finding and Fixing the Right Problem, LCE SEA Coaches Help Navy Sailors Learn New Skills and Save Maintenance Dollars
solutions
sectors
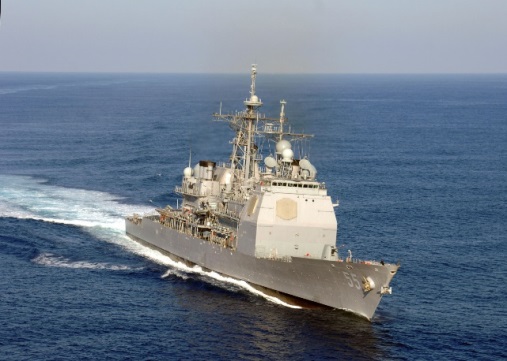
LCE SEA Coaches Help Sailors Diagnose the Right Problem and Save Money on Repairs
The engineering department of the U.S. Navy’s Mid-Atlantic Regional Maintenance Center (MARMC) directly supports Fleet and Type Commanders with waterfront technical and logistics services and maintenance training associated with the installation, operation, maintenance, and readiness of shipboard equipment and systems. The engineering group’s mission is to design, build, deliver and maintain ships and systems on time and on budget for the U.S. Navy. They are the leaders of the ship repair industry in all aspects of ship maintenance.
Air conditioning plants are systems that include a compressor, condenser, thermostatic expansion valve and an evaporator or chiller. These systems are installed on naval ships to cool chilled water, which is circulated throughout the ship to cool equipment and keep the environment comfortable. Ticonderoga-class cruisers have four 200-ton, 236FA centrifugal air conditioning plants. One of these cruisers was scheduled for a routine availability at a Norfolk, VA, shipyard. Prior to the availability, an LCE SEA Coach assigned to MARMC reviewed the work package of planned work for accuracy and completeness.
Reviewing work package for an upcoming routine availability identifies costly planned work that may not be the right solution to an air conditioning plant problem
During the work package review, the LCE SEA Coach found a line item for the overhaul of one of the air conditioning compressors. The ship was experiencing high lube oil temperatures during operation and showing signs of possible flow restrictions in the cooler circuit. These conditions plus a long-standing bearing oil temperature problem prompted the ship’s Maintenance Manager to submit a job for the air conditioning plant to be overhauled during the next Chief of Naval Operations industrial availability.
LCE SEA Coaches assigned to MARMC had previously provided problem-solving support for this issue and they were sure the problem was a low flow of chilled water through the lube oil cooler. They contacted the MARMC Project Support Engineer, explained that overhauling the compressor would not fix the low flow problem, and received authorization to conduct some additional testing and troubleshooting onboard the ship.
More thorough troubleshooting allows LCE’s SEA Coach to identify the correct problem and guide ship’s force through repair process, saving the Navy significant time and money
The SEA Coaches observed the operation of the air conditioning plant, provided troubleshooting guidance to the ship’s force operators, and oversaw the disassembly of the lube oil cooler and associated seawater inlet/outlet piping circuits. In the project debrief, the SEA Coaches left detailed step-by-step instructions for further repairs that were required.
The vessel’s Port Engineer reported that after ship’s force accomplished the actions detailed in the debrief, the air conditioning plant was operating within all parameters at full capacity. Identifying and fixing the correct problem – the low flow of chilled water – eliminated the need to overhaul the compressor, saving the Navy $350,000 in estimated maintenance costs. Under the direction of experienced LCE SEA Coaches, ship’s force personnel accomplished the work themselves, allowing them to gain experience in how to troubleshoot and repair their equipment when future problems arise.
About LCE
Life Cycle Engineering (LCE) provides consulting, engineering, information technology and education solutions that deliver lasting results for private industry, the Department of Defense and other government organizations. The quality, expertise and dedication of our employees enable Life Cycle Engineering to serve as a trusted resource that helps people and organizations to achieve their full potential. Founded in 1976, LCE is headquartered in Charleston, South Carolina with offices across North America and experience around the globe. Follow us on LinkedIn, Twitter and YouTube for company updates.
Contact Us
Corporate Headquarters
Life Cycle Engineering
4360 Corporate Road
Charleston, SC 29405-7445
843.744.7110
info@LCE.com