Implementing Reliability Excellence Yields Big Gains in OEE for a South Carolina Steel Company
solutions
sectors
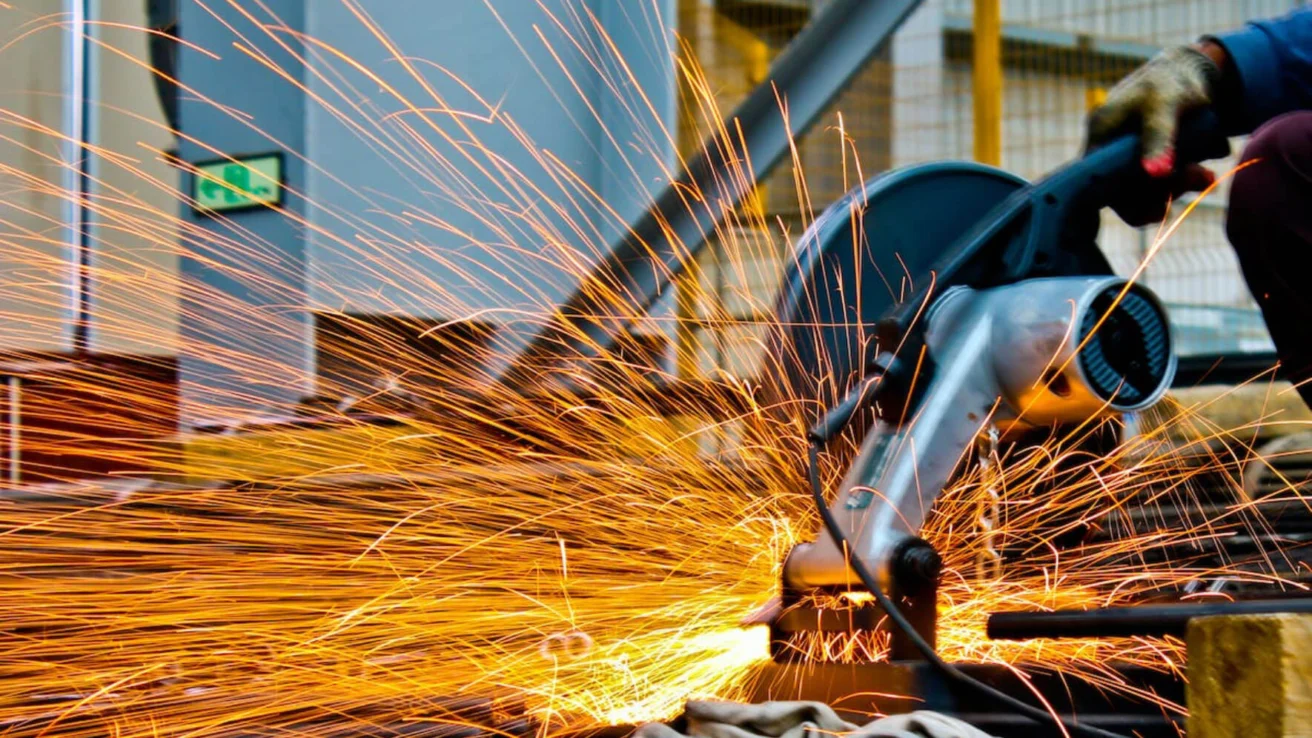
Implementing-Reliability-Excellence-Yields-Big-Gains-in-OEE-for-a-South-Carolina-Steel-Company-210
One of four mini-mills under a steel group based in SC, this company provides rebar, angles, channels, rounds, flats, squares and billets to customers throughout the southeastern United States. In the late 1990s steel imports started to rise significantly and several U.S. steel producers couldn’t compete, resulting in industry consolidation. With increasing competition from China, India, Russia and Europe, the company needed to operate more efficiently to remain competitive. They needed to improve Overall Equipment Efficiency (OEE), achieve asset design capacity, optimize material management and eliminate recurring asset failures. They also wanted to reduce frustration levels by fostering an operations/maintenance partnership and make sure that they could satisfy their customers’ needs on time, every time.
To accomplish their business goals, the steel company chose to partner with Life Cycle Engineering to help them implement Reliability Excellence (Rx). In addition to the return on investment that they anticipated, they identified other benefits of taking on an improvement initiative. For management it represented an opportunity to demonstrate leadership in order to improve operational and financial performance and leave a legacy of excellence. The anticipated benefits for employees included less frustration, greater job security, new skills and capabilities, and opportunities to grow and excel.
In late 2005, the steel company embarked on its Rx journey. Fully implementing Rx often takes three to five years, but they quickly started seeing results. OEE gain in 2005 was $621,000. In 2006, the increase in OEE grew to $790,000 and the 2007 OEE gain was in excess of $1.4 million.
Many elements contributed to these results including creating a partnership agreement between operations, maintenance and management, establishing metrics to monitor performance and developing an Rx Master Plan. Maintenance resources were restructured into a formal department to support new best practices processes, and roles and responsibilities were clearly defined. To implement the Master Plan, cross-functional focus teams worked on specific work streams for work control, planning and scheduling, materials management, production improvement and reliability engineering. Initiatives to sustain dramatic progress and continue improving included establishing a reliability engineering function, training the organization on root cause analysis, developing new management reporting capabilities, and scheduling re-assessments for auditing purposes.
The journey to Reliability Excellence is a challenging one. Moving from a reactive to a proactive culture requires leadership, a shared vision embraced by the entire organization, strong partnerships and the willingness to change behaviors and attitudes. This steel company has begun to reap the benefits and looks forward to competing successfully in an increasingly global world market.
© 2008 Life Cycle Engineering, Inc.
For More Information
843.744.7110 | info@LCE.com