LCE’s Experts Use Design and Engineering Skills to Redesign Critical Machinery Systems
solutions
sectors
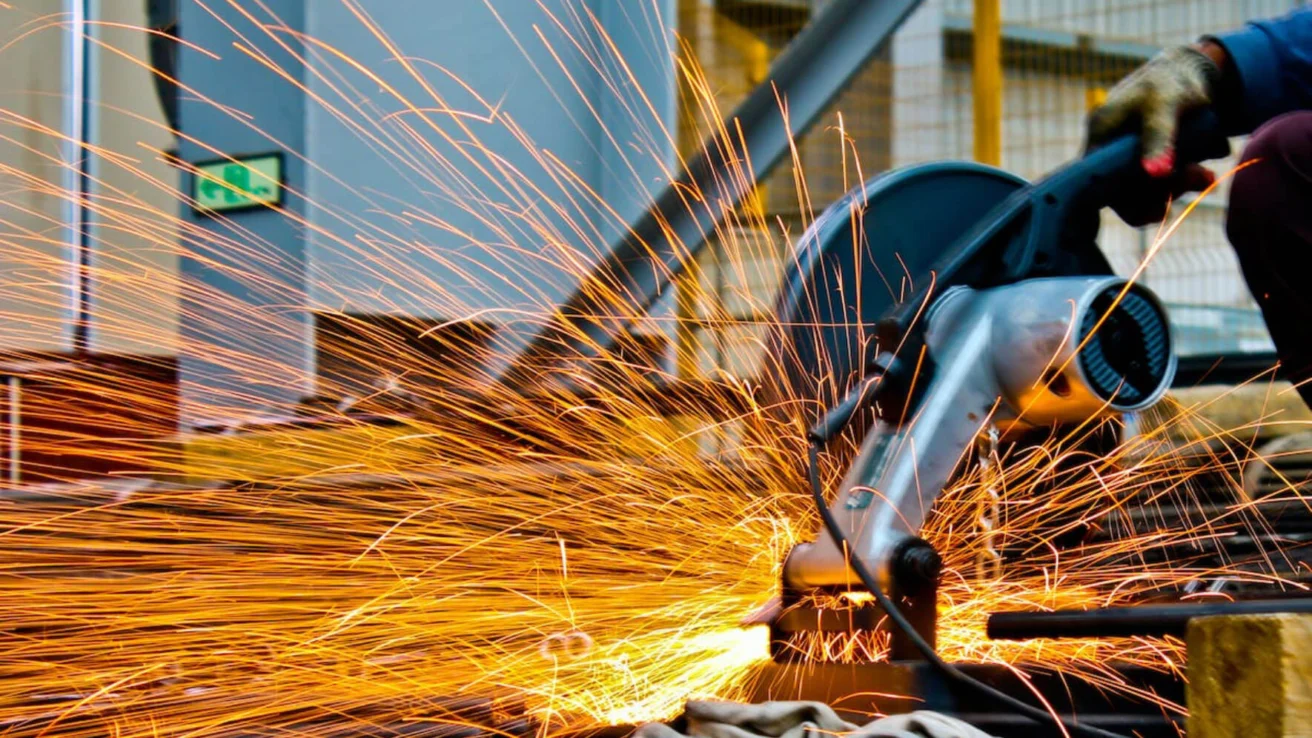
LCE Experts Help Redesign Critical Machinery Systems
Creativity. Talent. Know-how. Experience. Those are descriptors for the type of engineers you want helping to develop and test a working prototype. That’s why Life Cycle Engineering is a preferred partner when it comes to making the jump from a technology design to a working prototype. LCE’s engineering experts solve problems for clients from the U.S. Navy to market-leading manufacturers.
Helping Naval Surface Warfare Center Philadelphia Division (NSWCPD) Redesign Non-Combatant Craft Switchboards
The U.S. Navy uses the Improved Navy Lighterage System (INLS) to provide dynamic logistical support. The INLS resembles a floating pier made up of interchangeable modules. It’s used to transfer cargo from Military Sealift Command (MSC) ships to shore areas where conventional port facilities are unavailable or inadequate. The various pontoon sections can be assembled in a variety of ways to create a Roll-on/Roll-off Discharge Facility (RRDF). MSC prepositioning ships discharge equipment onto the RRDF, then onto lighterage, such as barge ferries or landing craft utilities, for transportation to the shore.
NSWCPD engaged Life Cycle Engineering to help redesign the non-combatant craft main switchboards in support of INLS operations. All machinery on a ship that consumes electrical power is connected to a switchboard or a power source that is fed from a switchboard. This integrated assembly of controls, equipment, measuring instruments and indicators is necessary for efficient control of the electrical systems and power-operated equipment.
Because of obsolescent breakers, the switchboards needed to be redesigned. LCE’s marine and engineering experts redesigned the switchboards with new breakers, bus bar, panels, and mounting frames and also successfully constructed mockups to validate the design prior to being installed on the craft.
Helping a Specialty Metal Manufacturer Upgrade Existing Machinery
A specialty metal manufacturer wanted to upgrade a high-speed annealing machine that was critical to its main production line for small parts. An existing version of the annealing machine needed to be redesigned to increase the processing speed to meet their customer’s increasing demands. Based on the reputation of Life Cycle Engineering’s team as effective problem-solvers, the manufacturer asked LCE’s engineering team to engage in their problem.
LCE used a three-phase design process to develop a working solution:
In the first phase, LCE provided conceptual designs of three feeder system concepts, using 3D CAD modeling software. The three designs were then down selected to one based on criteria for performance, operation, reliability, maintenance, and cost.
In the second phase, LCE performed the prototype detail design of the feeder system chosen from Phase 1. LCE’s engineers and designers developed detailed design drawings, bill of material, specifications, and cost estimates for the fabrication and assembly of the prototype.
In the third phase, LCE’s team successfully procured, built, and tested the feeder system prototype on the manufacturer’s annealing machine. LCE’s design met or exceeded the manufacturer’s performance requirements in all test cases.
The manufacturer has since begun to implement LCE’s feeder system design into their annealing machines and production line to meet their increasing customer demands.
For more information on LCE’s Engineering and Technical Services,
please visit the Life Cycle Engineering website.