Life Cycle Engineering Sharpens Maintenance Strategy for Premier Automation Manufacturer
solutions
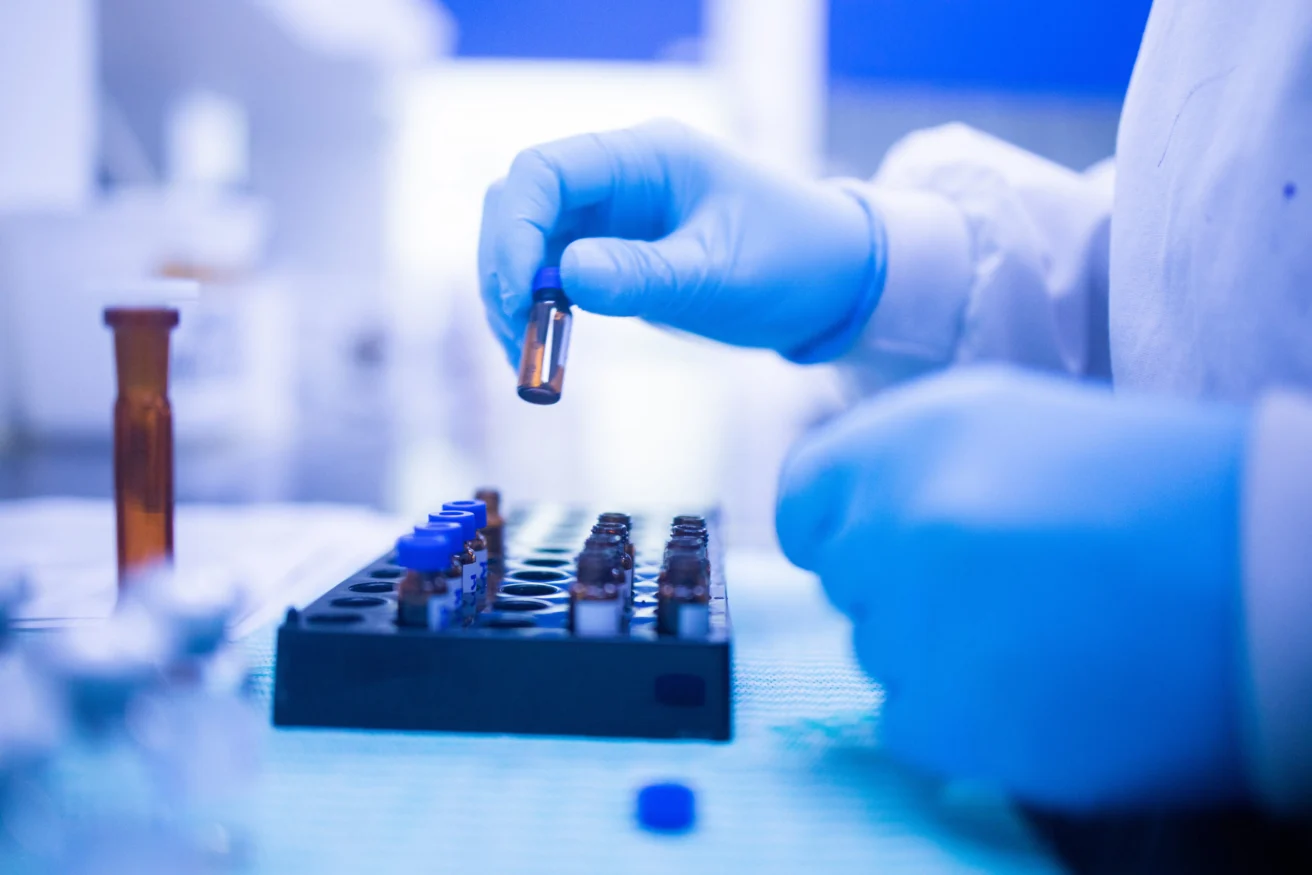
Life Cycle Engineering Sharpens Maintenance Strategy for Premier Automation Manufacturer
A major international pharmaceutical production line had a sound maintenance strategy in place for their custom-designed manufacturing solutions, or so they thought. However, at the request of their client, the business needed to re-think their risk-based asset management and equipment reliability analysis processes that would include a proven reliability-based preventive maintenance (PM) program. It was imperative for the manufacturer to have this put together as efficiently as possible because their work would soon begin on providing manufacturing equipment for an extensive plant upgrade and the launch of a new key product.
Putting the focus on preventive maintenance
To guide the delivery of a new PM strategy, the manufacturer partnered with Life Cycle Engineering (LCE) to oversee the development of the new failure mode-based PM plan. The objective was to review the current maintenance strategy in place for the manufacturer, evaluate failure modes of specific components and systems, identify vulnerabilities within the strategy that could potentially lead to equipment failure, and develop a new pilot program to be tested on a small section of the client’s line before being implemented for other key manufacturing and packaging lines at the site.
Developing reliability-based asset management
Over a span of three weeks, LCE reviewed the manufacturer’s design performance requirements, component design drawings, and operational parameters that would be used for their client’s upgrade. After reviewing, LCE constructed a detailed PM plan for one station of the client’s line that was based upon LCE’s equipment maintenance plan (EMP) format, which captures the relationships between specific component failure modes and corresponding maintenance activities. The EMP was slightly altered so that it would align with both the manufacturer and their client’s formatting and content requirements. Along with the development of the PM plan, LCE also created executable PM job plans to clearly state the maintenance requirements for each specific asset along with the actions that need to take place to properly maintain the integrity of the asset.
LCE provided additional off-site support and on-site staffing for two weeks. The support staff focused on mechanical aspects of the PM and job plan development, while other dedicated individuals concentrated on electrical, instrumentation, and control aspects.
Proving the worth of a sound maintenance strategy
After three weeks of support, LCE was effective in creating an enhanced maintenance strategy that included a sound preventive maintenance plan for the manufacturer. The strategy was tested on a small section of the manufacturer’s client line and the approach would go on to be fully implemented throughout the entire site, reassuring the client that all new manufacturing assets would operate effectively throughout their life cycle.
For more information about improving operational and financial performance, please email LCE at info@LCE.com or visit www.LCE.com.
About LCE
Life Cycle Engineering (LCE) (www.LCE.com) provides consulting, engineering, applied technology and education solutions that deliver lasting results for private industry, the Department of Defense and other government organizations. The quality, expertise and dedication of our employees enable Life Cycle Engineering to serve as a trusted resource that helps people and organizations to achieve their full potential. Founded in 1976, LCE is headquartered in Charleston, South Carolina with offices across North America and experience around the globe.
Contact Us
Corporate Headquarters
Life Cycle Engineering
4360 Corporate Road
Charleston, SC 29405-7445
843.744.7110
info@LCE.com