Pre-Startup Reliability Strategies for Carbon-Negative Materials Plant
solutions
sectors
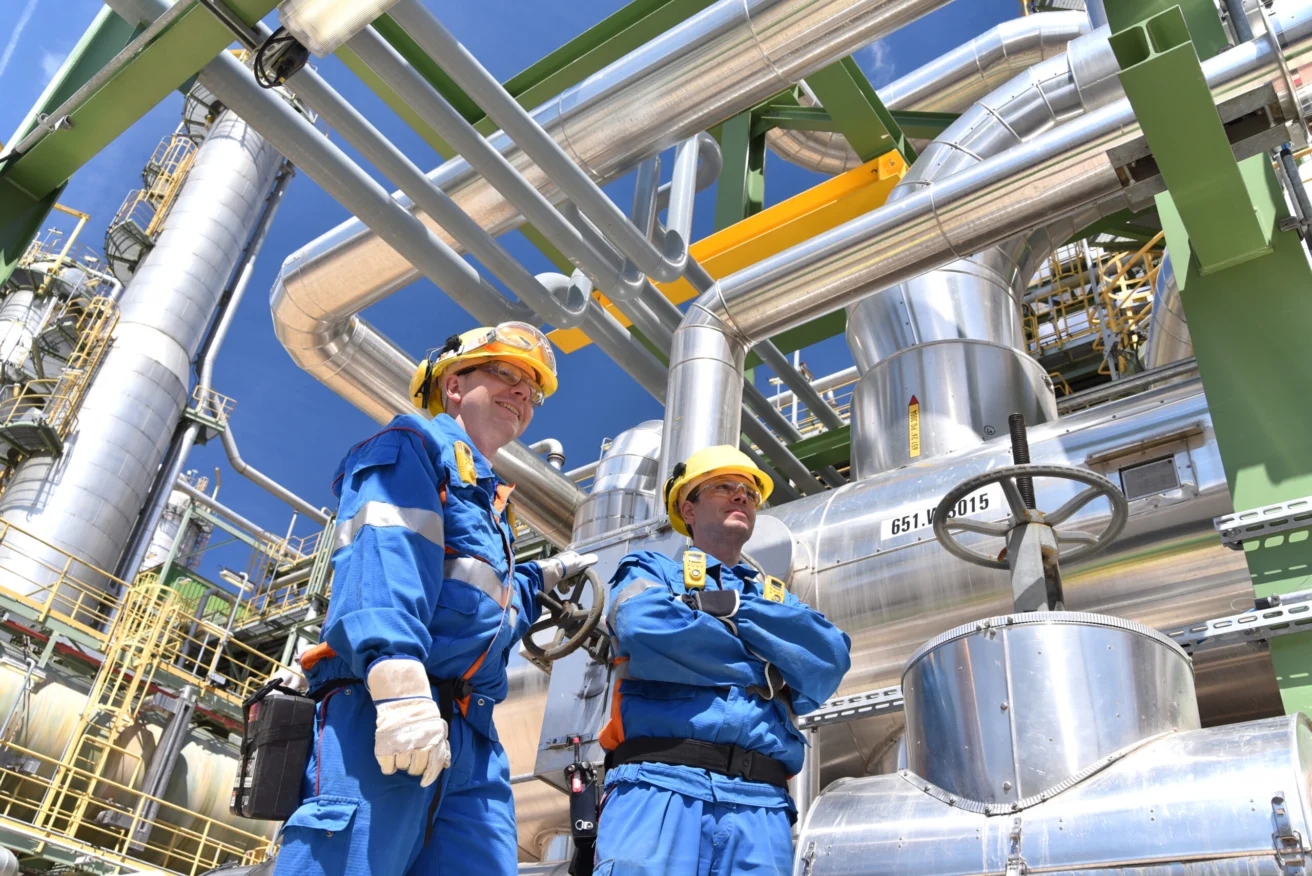
Intro:
As a leading carbon-negative materials company, this global leader is pioneering the development of technologies that drive the global transition towards more sustainable products.
Background:
The plant was in the early stages of constructing the first chemical plant of its kind. This plant would produce sustainable decarbonized materials for use in packaging, textiles, automotive – and more.
Issue(s):
This site faced a complex challenge: the development of a groundbreaking chemical plant with sustainability at its core. They needed to ensure that the plant’s assets and maintenance processes were optimized for efficiency and reliability. Additionally, they aimed to meet a strict startup schedule, requiring comprehensive analysis and planning within a relatively short timeframe.
Solution:
The project’s scope was extensive and encompassed two phases:
In Phase 1, the LCE team built equipment hierarchies, determined asset criticality, created Bill of Materials (BOMs), and performed Failure Mode and Effects Analysis (FMEA) on a critical reactor. We also developed standardized preventive maintenance job plans, laying the foundation for efficient maintenance practices. Additionally, we provided guidance on selecting the right CMMS to manage their maintenance work and storeroom inventory.
In Phase 2, our team’s expertise came to the fore as we conducted detailed Failure Mode Effect Analyses (FMEAs) for several key operating systems and auxiliary systems. This comprehensive analysis resulted in the development of preventive maintenance job plans tailored to these systems, ensuring optimal asset performance.
Impact:
The impact of our collaboration with this carbon negative materials company was substantial. Critical spare parts were procured ahead of plant startup, and all FMEAs and preventive maintenance plans for critical assets were completed. A CMMS was successfully selected, and plant commissioning commenced in early 2023, with Phase 3 scheduled for implementation after full operationalization. Phase 3 will consist of developing and implementing best practice Work Management, Reliability Engineering and Materials Management processes for use at the plant to optimize the efficiency and effectiveness of the workforce.
In summary, our partnership played a pivotal role in their mission to create sustainable materials and capture carbon in the process.
Our comprehensive solutions and expertise in maintenance and reliability engineering contributed to the successful startup of the plant, setting the stage for a more sustainable and carbon-negative future in materials production.
Quick Summary:
A leading carbon negative materials company faced the challenge of developing a sustainable chemical plant while adhering to a tight schedule. Our team tackled this challenge by:
- Determining critical assets and critical spare parts needed for those assets.
- Conducting detailed FMEAs for multiple systems, leading to tailored maintenance plans.
- Providing CMMS selection expertise.
- Implementing efficient maintenance processes, contributing to the successful operation of the plant and advancing sustainability in materials production.