Revised Material Inventory Practices Save Space, Time and Money
solutions
sectors
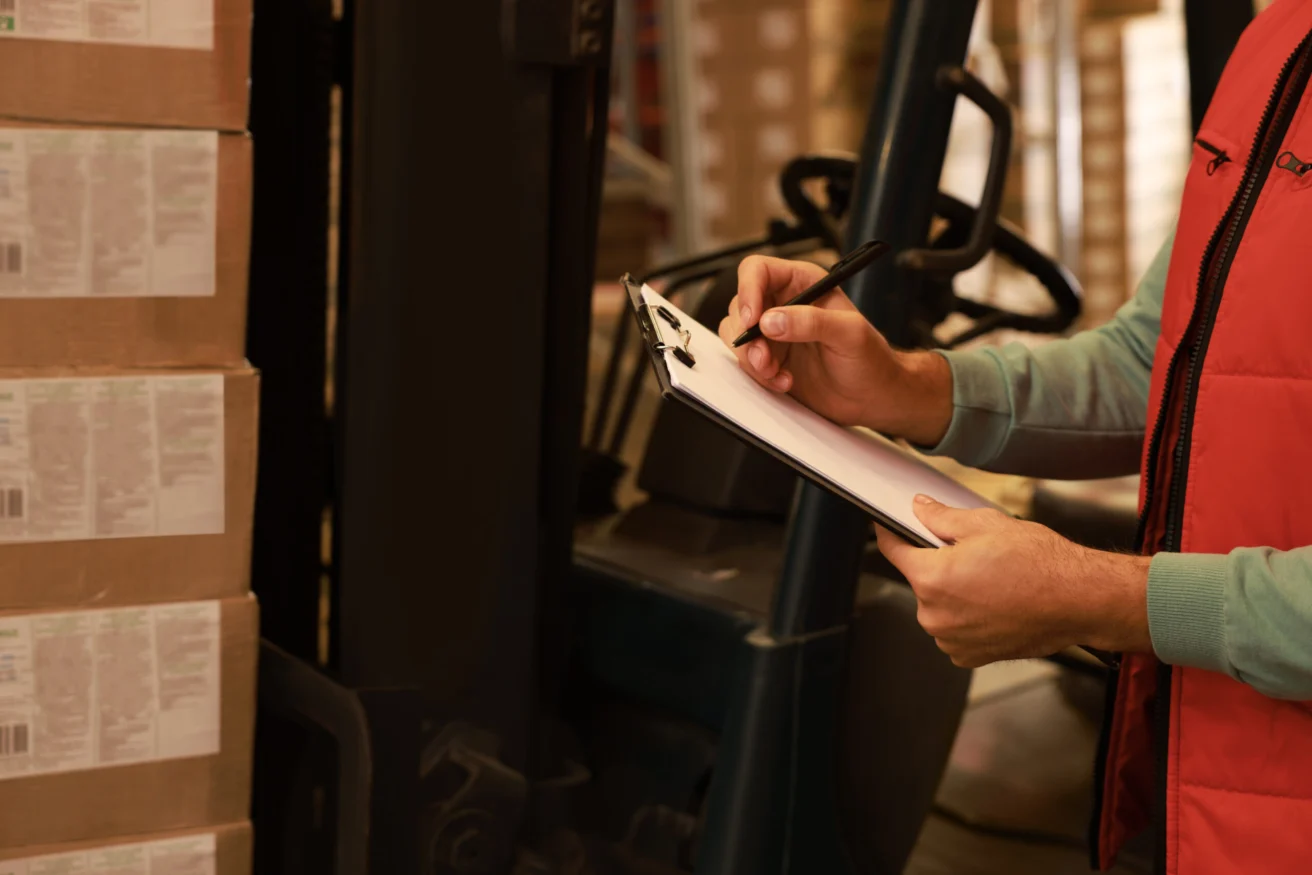
Download Revised Material Inventory Practices Save Space, Time and Money Success Story (PDF)
The Situation
A relatively small U.S. Navy expeditionary command had problems in the area of materiel inventory. Items were not being entered or tracked in an automated inventory data base. Materiel was being lost at great expense to the command. The equipment and supplies that did return from overseas were usually hurriedly placed in tri-wall boxes without needed identification or paperwork. This condition often prevented the required quick turnaround needed to provide the same materiel to the next sailors scheduled to deploy.
The Challenges
The Navy command was responsible for providing materiel items to deploying sailors from several separate units. Personnel assigned to the supply department were often called upon to deploy themselves, which prevented needed continuity and proper oversight.
Because items were often not entered or tracked in an inventory database, demand usage was not being registered in the Navy supply system. Significant demand is a requirement for the Navy supply system to identify the materiel and carry it as stocked materiel. Since it was not in the supply system, the items were often open-purchased, which is generally more expensive than standard-stocked materiel and lacks the documentation that stocked materiel has.
Many of these items are pilferable. Expensive items such as knives, combat boots, and sunglasses were often perceived by the sailors as being their own. When sailors returned from deployment, they often would simply keep the items and plan on using them when they next deployed. In turn, the command did not have the items for the next group of deploying sailors.
The Approach
With help from Life Cycle Engineering, the command:
- Established a team of supply personnel, headed by an LCE employee, to establish proper receipt, stow and issue procedures for all materiel items;
- Identified, barcoded, and entered all materiel items into an automated materiel management database;
- Implemented a standardized materiel location methodology;
- Developed a method for issuing material for deploying sailors through exterior CONEX boxes;
- Identified and disposed of excess material and identified and ordered materiel shortfalls
The Results
The command now has a standardized, automated process for receiving, stowing, and issuing materiel with appropriate storerooms where items are more easily identified and located. They also now have processes returning sailors to turn in government materiel. Major benefits of these management practices include:
- Identified and disposed of more than 600 line items of unused and obsolete materiel valued at over $400,000;
- Reduced the number of open purchases by 80%, which significantly reduced the amount of administrative time required by command personnel;
- Reduced average logistics response time (time it takes from a requisition to be placed in the supply system to materiel receipt) by 120%.
© Life Cycle Engineering, Inc
For More Information
843.744.7110 | info@LCE.com